涂料的缺陷与对策
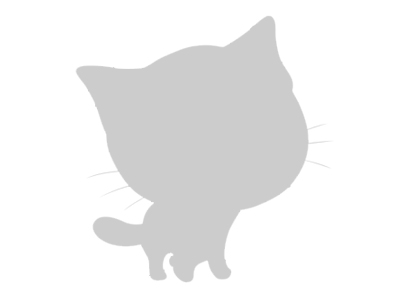
一、针孔
产生原因:
1、木材面素材调整不良,材面起毛,填充困难。
2、下涂之干燥不完全,即施与上涂,上涂急速干燥。
3、涂膜中还有尘埃、气泡、油漆粘度过高。
4、涂料与被涂面之温度差异过大。
5、加温干燥时,温度过高,静置时间不够,溶剂未充分挥发。
6、一次厚涂,表面干燥底层仍继续蒸发而突起。
7、使用不良的涂料稀释剂,或错误的涂料稀释剂。
8、反应涂料添加过量的固化剂,或错用固化剂。
9、涂料环境过高,或相对湿度过高。
排除方法:
1、素材的调整应彻底完全,砂光达到要求。
2、多次喷涂时,重涂时拉长待干时间,让下层干燥较充分。
3、涂装的作业物应予以彻底清理。
4、被涂物的表面温度和环境温度相同。
5、加热干燥的场合,涂膜的溶剂充分挥发后(静置时间延长)再施工。
6、避免一次过于厚涂,及调整适当的喷涂粘膜,底层与表面干燥一致。
7、使用时确认正确的稀释剂,及选用适当的稀释剂和涂料。
8、按指定的调漆比例正确调漆,并且充分搅拌均匀。
9、改善作业环境,并控制温湿度在适当的条件,或适当的添加慢干溶剂。
二、气泡
产生原因:
1、木材表面素材导管深,填充困难,发生气泡。
2、使用粘度过高的涂料。
3、喷涂之空气压力过高,涂料混入空气过多。
4、预热(加热干燥)过于激烈,或急剧加热。
5、涂装表面附着油分、灰尘、汗水等,这些不洁物周围集结水分。
6、压缩机及空气管内有水分,或设备发生水溅到作业物上面。
7、大部分与针孔发生原因一样
排除方法:
1、导管较深的素材事前作填充后喷涂。
2、适当的调整涂料的粘度。
3、调整适当的空气压力,减少空气的混入。
4、加热干燥时,静置时间需控制,充分挥发后施行。
5、涂装表面时注意表面的清洁,避免污染不洁物质。
6、定时泄掉压缩机水分及加装油水过滤器。
7、参考针孔对策。
三、鱼眼、火山口、开花
产生原因:
1、被涂料物中有水份、油性或油性蜡等。
2、涂料中有水、油份(空压机为主因)
3、作业场所被污染,或用油性蜡污染了环境和作业物。
4、使用过多的添加剂,或涂料不良及使用过期的涂料。
5、污染的布,抛光场所的油性蜡。
6、下涂涂料或着色剂品质不良,或被污染。
7、充满溶剂气体的场所,作业场所排气不良。
排除方法:
1、被涂物避免污染,且需砂光彻底。
2、水墙和流水墙保持清洁,流水顺畅,避免跳水,空压机油水也应注意。
3、作业场所、器具避免污染油份,蜡油等,手指、衣物污染应清洁后才可触碰作业物。
4、涂料保存超出储藏日期期限时应检查是否变质。
5、涂装时远离有污染地区,被污染之碎布应清理。
6、注意涂料中是否含有其他的杂质。
7、作业环境注意充分排气。
8、旧涂膜喷漆前用溶剂擦拭干净及再予以砂光,后再予以喷涂。
9、严重鱼眼发生时可用鱼眼防止剂添加于涂料中。
四、粗糙涂膜
产生原因:
1、喷涂是粘度过高。
2.、使用过高沸点的溶剂稀释剂。
3、喷涂距离不当或过远,喷枪或机器故障。
4、涂装室内环境过高。
5、超喷之半干燥涂膜,涂料附着(在角落或背光侧面此现象较多)
6、被涂物附着灰尘或环境灰尘太多。
排除方法:
1、调整适当的涂料的粘度。
2、使用适当指定的稀释剂与溶剂。
3、熟练喷涂技术与喷枪的使用正确操作,定期保养机器。
4、调整室内温度。
5、要避免喷涂则需训练操作者的喷涂技术动作、姿势等。
6、喷涂场所应保持清洁,尽量避开污染地区。
五、吸陷、目陷
产生原因:
1、使用不合适的稀释剂(溶解力太强)。
2、下涂涂膜不足,形成多孔的场合。
3、下层涂料未干燥充分,或未干燥即予以打磨。
4、打磨时使用太粗型号的砂纸。
5、上涂粘度太低,或涂布量不足。
6、使用品质不良的涂料。
7、被涂物表面附着灰尘、漆粉未清除。
8、素材之补土填充不良,或含有水分过多。
9、下涂一次后涂,致底层干燥不充分(或重涂时间过快)
排除方法:
1、慎重选择品质良好的稀释剂。
2、下涂涂膜应足够,砂光后应完全平坦无孔。
3、涂膜应充分硬化或干燥再施予上涂。
4、砂光纸型号应选择适合上涂细度的砂纸。
5、调和正确适当粘度涂料,均匀的涂布量。
6、使用品质好的涂料,喷涂前须清理被涂物表面。
7、涂装前素材处理须确实砂光,填充补土,木材含水率需适中。
8、涂装要领需分多次薄涂且控制间隔拉长,使下涂充分干燥。
六、橘皮肌
产生原因:
1、喷涂时,雾化的涂料粒子附着在涂膜表面不能流展平滑。
2、喷枪调整及喷涂技术问题,空气量多,距离太远。
3、工场温度太高,干燥过快,不能流展平坦。
4、用喷枪吹干表面,涂料粒子不能充分流展。
5、使用沸点低稀释剂,涂料粒子抵达涂面前即干燥。
6、涂料粘度过高时,或一次厚涂。
7、涂料无充分搅拌混合,影响起流展性。
8、表面不清洁,附着蜡、油分等不纯物。
9、作业环境有风,且风速过大。
10、涂料本身性质不合。
排除方法:
1、喷喷枪性能应保持良好状态,充分熟练喷枪使用方法,做适当的调整。
2、改善涂装工场温度。
3、使用适当的稀释剂。
4、不可厚涂,以中程度涂布量,调整适当粘度喷涂。
5、涂膜表面及里面均要充分干燥。
6、调整使当的涂料粘度,过高或过低都不好。
7、涂装前涂料应充分搅拌均匀。
8、防止在有风处涂装。
9、选择适当流平性较好的涂料。
10、涂膜处理:改进操作技术,重磨平坦再涂装一次。
七、喷涂漆痕
产生原因:
1、喷枪的喷幅展开不良的情况。
2、喷漆的运用技术不佳,喷涂时重迭不充分、不均匀。
3、面漆调漆时无充分稀释搅拌。
4、对遮盖力低的面漆,下层的颜色选择不当。
5、使用不当的稀释剂。
6、被涂物的表面太热或太冷的情况。
排除方法:
1、确实保养喷枪于正确使用状态,与正确调整喷幅适合喷涂。
2、涂装运行方式需正确,喷涂重迭需均匀。
3、使用良好的稀释剂,调漆时充分搅拌。
4、稀释色浓度,或减低一次的涂布量,或选择适当的下层涂料。
5、调整室内温度。
八、砂纸伤痕
产生原因:
1、素材砂光,逆木纹砂光而出现逆砂痕。
2、使用过粗的砂纸(布)砂光,或研磨方法错误。
3、涂膜没有干燥即加以研磨(尤其是两夜型涂装较明显)。
4、使用太慢干溶剂,致涂膜无法在一定时间干燥。
5、上涂涂膜太薄,及粘度过低。
6、砂光后未彻底清洁,涂料无法渗透。
7、砂光纸使用时因表面滞留漆粉,某部位已无砂光功能,会形成移动痕迹。
排除方法:1、选择最适合的砂光纸型号,一般第一次粗砂光,第二次砂光纸型号较细,并应将第一次之砂痕磨掉,以此类推。
2、砂光时应按木材纹理方向顺木纹砂光。
3、涂膜应于干燥后研磨,并除去灰尘漆粉。
4、使用砂光机或手持砂纸研磨并应考虑其砂纸型号。
5、砂纸使用一段时间后检视是否留漆粉,予以更换。
6、研磨的方向,动作要正确并检查。
7、涂料的粘度应予以适当的调整,喷涂厚膜应足够,足以覆盖砂痕。
8、视情况可先涂一层底漆,而在短时间内涂予面漆,增加膜厚。
9、使用在设定时间能使涂膜干燥研磨的稀释剂。
九、下炊、垂流、挂流
产生原因:1、加入过多的稀释剂,使涂料的粘度降低。
2、一次喷涂过高的涂布量,尤其在较慢干的涂料更易发生。
3、喷涂时的距离或角度或重迭不适当,使涂料分布不均匀。
4、喷涂时喷枪移动速度不适当,或慢或喷射幅歪斜,空气压力过低,漆量过高与空气量不搭配。
5、喷枪保养不当,孔道变形,或部分孔道阻塞以致漆形不良。
6、使用过高沸点的溶剂及稀释剂,因而干燥过慢。
7、温度高,温度低,干燥迟缓的场合。
排除方法:1、调整适当的涂料粘度,立面的喷涂时粘度稍可以增加。
2、适当的涂布量,避免第一次喷涂过厚,但仍需喷湿且膜厚均匀。
3、熟练喷枪的调整,其运行方法、角度、速度等,及彻底保养喷枪。
4、使用适合的稀释剂调和涂料。
5、室内温湿度充分予以考虑。
6、在照明良好的场所喷涂,许多流漆是因为视线不良所引起的。
十、细粒皱纹
产生原因:1、涂装时涂料粘度过高。
2、使用不当的稀释剂、溶剂(溶解力)
3、喷涂距离不当,空气压力过大。
4、环境风速过大,或温度高干燥过快。
5、涂料干燥就快或涂料的问题。
排除方法:1、调整使当地涂料粘度,延展性最适当的程度。
2、使用品质良好的稀释剂、溶剂与涂料。
3、调整使当的空气压力,并且加强涂装技术。
4、室内温湿度充分予以考虑。
5、在照明良好的场所喷涂,许多流漆是因为视线不良所引起的。
十一、粒状涂膜
产生原因:1、涂料树脂或添加剂、颜色、颜料的固块。
2、涂料的夹杂物、异状物、硬化颗粒等直接涂布,附着在漆膜上。
3、固化剂添加过多或调和搅拌不均匀。
4、涂料储藏过久超出安全使用期限、凝胶或涂料分散不均。
5、尚未指触干燥,空中的飞絮砂粒附着。
6、涂布时被涂物本身污物吹出,附着于漆膜中。
7、置物架等不清洁,于漆膜未干时移动或震动,灰尘污物掉落湿涂面。
8、使用溶解力较差的稀释剂,无法充分溶解涂料,或错用不当的稀释剂溶剂。
排除方法:1、一般涂料过期会产生胶固块,会影响涂料特性,应不再予以使用。
2、涂料的容器应彻底清理,涂装面漆时应予以过滤。
3、两液型涂料之主剂、固化剂调配比例需正确,并充分搅拌均匀。
4、使用涂料时应检视品质,是否含有固块或夹杂物。
5、作业场所应经常予以清扫,并应避免污染源。
6、作业的置物架、喷台、排气设备、输送带等应经常保持清洁无尘。
7、抽排风设备吸尘需良好,减少涂料雾化粒子及灰尘的停留。
8、涂装的表面喷涂之前应彻底清理,擦拭干净。
9、在同一场所避免同时做其他工作,并闲人勿进。
十二、回粘
产生原因:1、慢干溶剂添加于涂料中过多,溶剂无法挥发出来。
2、反应型涂料的固化剂添加量不足。
3、涂面被污染不洁。
4、空气不流通,受热气侵袭。
5、气候突变,雨季施工,湿度高。
6、性质不同涂料未干即施上涂料或混合使用。
7、上涂涂料硬度不够。
8、涂膜厚涂或多次重涂,漆膜未干燥即行包装重迭。
9、使用品质不良的涂料。
排除方法:1、选择适当干速的溶剂稀释剂,并且不可过量添加。
2、固化剂添加比率应正确,不可以过少(也不可以过多)。
3、保持涂面不被异物污染而再施行上涂。
4、涂装完成的待干漆膜,应置于通风良好的地方,让溶剂充分挥发。
5、在不良的气候施工时,置放时间应加长,或加温干燥。
6、选择不同涂料时,应待下层充分干燥后再上涂,不同涂料千万不可混使。
7、上涂面漆视需要使用适当硬度的涂料。
8、测试厚膜涂布多少次,待干时间需多久才可重迭,包装出货。
十三、龟裂、裂纹
产生原因:1、木材含水率过度,致使下底收缩。
2、涂装时一次过度的厚涂。
3、下层漆未干燥充分,即进行上涂。
4、固化剂添加过量,或用错误的固化剂。
5、上下层不同种类的涂料,性质不合。
6、涂料不良,缺乏伸张性。
7、已有裂痕的旧涂膜再涂上新的涂膜。
8、使用品质不良的稀释剂,或随意添加添加剂、颜料。
排除方法:1、木材含水率应干燥至10%以下。
2、适当的涂布量,多量多次,并充分干燥,间隔干燥充分。
3、调漆固化剂比率应按指定的来正确调漆。
4、正确了解不同种类涂料的搭配,慎重选择、判别。
5、选择信誉品质良好的涂料。
6、已经有裂痕的涂膜需除去裂痕才可再喷涂,不可直接喷涂。
7、使用适当指定的稀释剂,非专业人员不需另添加其他涂料。
十四、剥离、离层
产生原因:1、被涂物表面不洁,附着油、水、灰尘、蜡、手垢、清洁液等。
2、涂料性质不良,容易收缩;涂料搅拌不均,使用它不良稀释剂。
3、被涂物光滑度高,附着力差,或下层喷漆已干燥硬化,涂膜研磨不充分,即予以喷涂(尤其两液型涂料硬化后未砂光)。
4、涂料中渗进水份、油份。
5、下涂涂料与上涂涂料性质不合。
6、下涂未充分干燥即进行中涂
7、涂装时未按指定工程涂装施工。
8、使用过期的涂料或固化剂添加量过高。
9、两液型涂料超出可使用时间过久已变质。
排除方法:1、被涂物应不要污染,并需使其清洁。
2、慎重选择涂料,(尤其需要厚涂的涂装),并于涂布前充分搅拌。
3、涂装前均能砂光(尤其需添加固化剂涂料)充分,使其增加附着力。
4、涂料中严防渗入水份、油份等异物。
5、不使用不同性质涂料,使用适合重涂的涂料。
6、充分干燥涂膜再施与中涂。
7、按指定涂装工程施工。
8、两液型涂料固化剂不可超量,过期涂料检查是否变质。
9、不使用已超出可使用时间的涂料(两液型混合后的时间)。
十五、色分离
产生原因:1、涂膜过厚,尤其是一次厚涂或下层颜色未干重涂。
2、稀释剂溶解力不足。
3、调和涂料搅拌不均匀。
4、添加过量的稀释剂,粘度过低,延展过度。
5、颜料分散不良。
排除方法:1、适当的涂布量,及低层颜色干燥后再涂布。
2、使用指定的稀释剂。
3、充分搅拌涂料。
4、调整到不会产生颜色分离的粘度。
5、选择品质良好的涂料或着色剂。
十六、光泽不均
产生原因:1、喷射幅重叠不均匀,过多或过少。
2、喷枪、喷嘴有残留油漆附着,吐出量不均一。
3、喷射幅雾化不完全,喷枪移动不正确。
4、操作不当,技术欠佳。
5、涂料品质欠佳。
排除方法:1、注意喷枪操作,走枪正确。
2、清洗喷枪,平时做好保养。
3、调整及检查喷枪。
4、训练纯熟的喷漆技术员。
5、使用良好品质的涂料。
十七、变色
产生原因:1、紫外线直接晒或其他物质附着。
2、固化剂添加过量或涂料储存过久。
3、使用易褪色的着色剂、颜料、染料。
4、高温干燥时变色(UV紫外线涂料有此变色的)。
排除方法:1、应使用能抗紫外线之涂料,尤其白色或浅色涂装。
2、适量正确的固化剂比例。
3、涂料储存过久不应予以考虑。
4、使用适当较不易褪色着色剂。
5、紫外光硬化涂料应选择不褪色着色剂。
十八、不干
产生原因:1、被涂面含有水份、油份或蜡质等物。
2、酸、碱性固化剂或颜料、染料合并使用。
3、固化剂使用错误或比例不对,以及稀释剂使用错误。
4、涂料中混入水份、油份。
5、温度过低,未达到干燥条件。
排除方法:1、保持被涂面之清洁。
2、使用固化剂事前应确认,并正确调和比例,和指定稀释剂稀释。(依各夜之调和比及种类比率不同确认)。
3、废弃超出指定可使用时间之涂料,或含有水份、油份的杂质涂料。
4、在正常室温内喷漆。
5、调漆时应搅拌均匀,使能正确达到干燥。
6、涂面若无法干燥(加热),则应将涂面完全去除。
十九、白化
产生原因:1、空气高温高湿,相对湿度高于80%以上时,一把汗夏天下雨常见。
2、被涂物或容器含有水份。
3、稀释剂沸点太低,挥发过快或混入水份。
4、空气压缩机或空气含有水份。
5、涂膜含有水份未清除干净。
排除方法:1、降低室内温度,避免在高温环境中涂装作业,或适量使用慢干溶剂。
2、容器与涂料避免混入水份,涂料稀释剂避免与露天存放会侵入湿气。
3、空气压缩机应加装水份过滤器,并定时泄掉水份。
4、湿度高时应避免厚涂。
5、发生白化现象立即停止作业,然后予以修正。
6、轻度的白化可以喷涂后加热干燥。
7、注意周围环境、设备等避免被涂物粘膜粘水。
二十、光泽不良
产生原因:1、被涂物多空粗糙,或涂膜不足吸陷,或附有油、水份不纯物。
2、上涂涂膜不足或采用干喷,喷涂的压力过大,粘度过低。
3、干燥室换气不良,溶剂蒸发的气体污染空气,漆膜白化。
4、稀释剂的品质不良,或稀释剂的沸点低干燥过快。
5、抛光的涂装,未充分干燥及研磨抛光,或抛光蜡太粗
6、在湿度高、低温度的涂装场合。
7、喷的部位或白化部位。
8、用品质不良的涂料涂装。
9、砂光粗糙,或漆粉灰尘未除干净。
排除方法:1、被涂物砂光平坦细腻,并清除表面不洁物质。
2、控制适当的涂料粘度,以正确的方法喷涂适中的厚膜。
3、干燥室的干燥过程中,保持良好的换气。
4、选择适中干燥的稀释剂。
5、涂膜应完全干燥后才可以进行抛光工作,并选择蜡的细度。
6、要有良好的涂装作业温湿度。
7、训练喷涂方法,并且熟知作业物的喷涂方式。
8、注意选用品质好的涂料。
9、使用较细度的砂纸砂光,喷涂之前表面应确实清理。
二一、变黄
产生原因:1、涂料不良,未使用非黄变涂料
2、环境因素、空气、水等。
3、日晒涂膜老化分解。
4、高热干燥。
排除方法: 1、慎重选择涂料,使用非黄变涂料。
2、对家具应勤予保养,经常打蜡保护。
3、尽量不要直接日照,黄变仍时自然现象,选择非黄变涂料可减轻。
4、加热不可过量。
二二、皱纹
产生原因: 1、表面干燥过快,涂膜干燥不均一。
2、一次厚涂,只在表面急速干燥,不能同时干燥,下层松弛上层紧绷。
3、大热天异常高温,或直接照射环境。
4、下涂干燥不完全,即行上涂作业,并急急的将上涂强制干燥。
5、下涂及上涂的涂料组合不当,上涂料的稀释剂溶解力太强,硬化不完全的PU、AA涂膜上,涂布拉卡,或在NC涂膜上涂布PU、AA涂料。
6、固化剂调配不当。
7、第一层涂膜在半干或聚合硬化不完全,而施与第二道涂膜。
8、下涂涂膜无充分研磨,即施与上涂。
排除方法: 1、使用较慢干的稀释剂,和适合溶解力的溶剂。
2、调节适量的涂布量。
3、避免在异常高温下涂装。
4、绝对禁止超厚膜,每次喷涂间要让溶剂充分挥发。
5、使用性质相合的涂料,避免较软涂料在下层。
6、涂装后需静置指触干后方可加温干燥。
7、两液型或多液型涂料,固化剂需调配正确及搅拌均匀。
8、在使用不同或同类涂料时,下涂应使其硬化干燥。
9、聚合型干燥涂膜,干燥后砂光应尽量充分。
本网站仅为行业交流分享平台,转载请尊重原作者权益,如需转载请注明中华整木网(www.cnzhengmu.com)