木材干燥工业现状与发展趋势
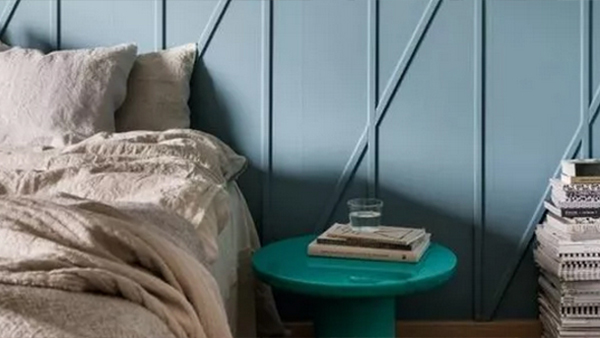
作为全球第二大木材消耗国和第一大木材进口国,近10年来中国木材消费总量增长了173%,目前全国年木材消耗量达6亿多m3。2017年全国范围内已全面停止天然林商业性采伐,目前国内木材工业所需原料的对外依存度超过55%,而世界主要木材出口国纷纷禁止或者严格限制原木出口,因此除积极开拓新的木材进口来源地外,提高现有的木材加工利用水平,降低木材加工过程中的损耗,提高产品质量和使用周期是缓解现阶段木材资源供应紧张的重要途径。在木材生产加工过程中,木材干燥是提高木材利用率,保障木制品质量最有效的措施之一。
按照木材用途及使用地木材平衡含水率情况,将木材干燥至一定含水率可有效保证木制品使用过程尺寸稳定,防止木材腐朽,显著降低运输成本。自20世纪90年代我国木材工业进入高速发展阶段,经过近30年的发展与经验积累,我国木材干燥工业水平发展到了一定高度。从总体上看,我国木材干燥设备、干燥工艺、干燥理论与技术水平都与欧美林业发达国家差距不大。但伴随着产业发展与升级,我国木材干燥工业也存在一定问题。笔者对我国主要制材加工区域及代表性制材干燥加工企业进行调研后,总结了木材干燥工业现状及存在的主要问题,分析发展趋势并提出建议,以求促进我国木材干燥工业的发展。
1、我国木材干燥工业现状及存在问题
1.1 木材干燥工业原材料对外依存度高
木材干燥生产原料一般特指锯材,其来源于原木。根据统计数据,2017年我国进口原木5 539.8万m3,同比增长13.7%,进口锯材3 739.3万m3,同比增长18.7%。进口木材中针叶树材占总量68%,阔叶树材占比32%(其中热带阔叶树材占21%、温带阔叶树材占11%)。进口针叶树材目前主要来源国为新西兰、俄罗斯、美国、澳大利亚、加拿大等国,主要树种为辐射松、樟子松、落叶松等,其中特别值得一提的是新西兰已超越俄罗斯成为我国原木进口量最大来源国,2017年从新西兰进口原木共计1 436.4万m3,占我国原木进口总量25.93%,主要树种为辐射松(Pinus radiata)。辐射松是一种速生、高产和多用途树种,其原产于美国,19世纪被引入新西兰,由于其科学栽培管理,可持续稳定供应,是我国今后最重要的用材树种之一。
国产材中能够用做锯材且稳定供应的树种较少,以人工林速生树种木材为主,主要包括杨木、杉木、马尾松,但这些木材一般材质较差,用作锯材附加值较低,产量也较少。目前也对一些材质较好的树种进行定向培育,主要树种包括北方栎类、华北落叶松、相思木类、樟木、楠木等树种,这些树种的木材均具优良材性,且已进入推广种植阶段,是今后木材干燥生产值得关注的储备原材料。
1.2 木材干燥方法多样化,但规范化生产比例较低
木材干燥方法种类很多,目前生产中实际应用的干燥方法主要有常规蒸汽干燥、高温干燥(包括过热蒸汽干燥)、热泵干燥(除湿干燥)、太阳能干燥、真空干燥、高频干燥、石蜡油干燥等,以及企业结合自身情况将不同干燥方法进行结合的联合干燥,如常规-高温干燥、常规-热泵干燥、太阳能-热泵干燥、真空-高频干燥等。
由于常规干燥技术成熟、操作简便、装材量大等优点,目前仍占干燥生产主导地位。需要说明的是本文所述的常规干燥特指周期式常规干燥,待干锯材一次性装窑,干燥完成后同时出窑(图1、图2)。除周期式常规干燥外,近些年连续式隧道干燥窑应用也越来越多,这种干燥方式适用于大批量单一树种或材性较接近的树种,国内部分企业将其用于辐射松等锯材的干燥生产。
热泵干燥是近年来备受关注的干燥方法,由于环保压力不断提升,部分地区生物质能源也纳入限制使用范围,因此常规干燥所需的蒸汽来源受到影响。一些生产规模较小的木材加工企业,受生产限制影响转而使用热泵式干燥窑。根据对相关企业的调查走访,目前热泵干燥已成为中小型企业关注的热点,今后应用该方法的企业数量会进一步增加。
同样受环保与生产成本影响,太阳能干燥也成为企业关注的干燥方法,但由于太阳能受昼夜、季节等因素影响较大,因此企业多采用太阳能-热泵、太阳能-常规联合干燥的方式进行生产,且目前多用于单板、薄板的干燥。真空、高频等干燥方法,由于成本较高目前仍多用于珍贵材加工企业,且一般采用真空- 高频联合干燥的方式。石蜡油干燥也多用于珍贵材的干燥,该方法除保证干燥效率,同时也提高了木材的尺寸稳定性,但有些企业所用的石蜡在木制品使用过程中有较多的挥发物散出,企业应注意石蜡的选择。
图1 常规蒸汽干燥窑
总体而言,现阶段木材干燥生产方法多样化,干燥生产能力较以往显著提升,但规范化生产比例较低。
对于大多数企业而言,制材与干燥生产一般为独立外包制,企业管理者无法进行科学有效的管理。多数干燥窑操作工人不具备专业知识,也未经上岗培训,干燥窑操作全靠经验,干燥质量难以保证,干燥周期较长。以辐射松为例,目前50 mm厚锯材普遍干燥周期接近两周,后期最高干燥温度一般不超过85 ℃,但经优化后干燥周期普遍可缩短三分之一左右,而如果采用国外普遍采用的高温干燥方法,干燥周期可缩短至5天以内,显著提高效率。
图2 常规蒸汽干燥窑
1.3 木材干燥生产能源结构调整,干燥成本不断提高
如前所述,随着环保要求不断提高,企业中4 t/h小型燃煤锅炉必须关停,一般木材加工企业不具备使用大型锅炉的条件。以往很多企业生产过程直接将木废料作为锅炉燃料,部分企业购置生物质颗粒挤压机,将木废料制成生物质颗粒以提高燃料能量密度,但目前很多地区也将生物质颗粒作为限制性燃料,一旦环保紧张时,使用生物质颗粒燃料锅炉的企业同样面临停工的风险。山东、河北、江苏、浙江等地区已经加快了煤改气进程,企业干燥成本明显提高。以山东地区某大型辐射松制材干燥加工企业为例,采用煤炭与木废料作为燃料时,每立方米辐射松干燥成本约为120元,以生物质颗粒作为燃料时,每立方米干燥成本上升至180元,采用天然气作为燃料时每立方米干燥成本在260元以上,企业生产成本急剧上升。
1.4 木材干燥集约化、规模化生产是发展方向,但现阶段中小型企业数量占比仍偏高
国外制材干燥加工企业很早便以集约化大规模生产来提高生产效率、保证生产质量,同时降低成本。一般的制材干燥企业年消耗原木量在30万m3以上,欧洲大型现代化锯材加工厂年消耗原木量更是可以达到200万m3以上,这些企业都建有自己的能源中心,不但解决了木材干燥生产所需的蒸汽,同时消耗了木材加工剩余物,降低了生产成本。
国内相关木材加工企业经历了多年发展,同时受到国家相关政策的引导(如国家级木材加工贸易产业区),木材干燥集约化、规模化生产比例明显提高,在一些临港区域产生了一批有代表性的大型木材加工企业,如山东临沂、日照、潍坊,江苏镇江、盐城,福建漳州等地区,单个木材加工企业年消耗原木量可达30 万m3,建有干燥窑数量达到200间以上。虽然大型木材加工企业数量有一定增长,但现阶段中小型木材加工企业数量占比仍然偏高,根据相关行业从业人员提供的数据,以山东临沂、日照地区辐射松制材干燥加工企业为例,年消耗原木量1万m3以下的企业占比超过80%,产业规模结构仍有待转变。
1.5 木材干燥生产全自动控制、远程控制进一步发展
木材干燥生产全自动控制、远程控制一直是干燥设备最理想的控制模式。随着国内干燥技术与干燥工艺发展,在干燥树种相对稳定的前提下,干燥设备可采用全自动控制进行生产,目前已有很多企业采用该种控制模式。相较于早期的干燥窑控制系统,目前全自动控制系统已更加成熟,最新的控制系统已经可以通过手机进行远程控制,更有益于控制木材干燥生产过程。
针对上述问题,作者对我国木材干燥工业的发展提出以下建议:
1)木材干燥生产应借鉴国外生产经验方法与干燥工艺
2) 以常规干燥为主,多种干燥方式协同发展
3)企业应发展集约化、规模化生产,淘汰落后产能
4)提高干燥设备质量,进一步扩大全自动控制和远程控制系统的应用
本网站仅为行业交流分享平台,转载请尊重原作者权益,如需转载请注明中华整木网(www.cnzhengmu.com)