精益生产 | 这是一条家居企业无法回避的“救赎之路”
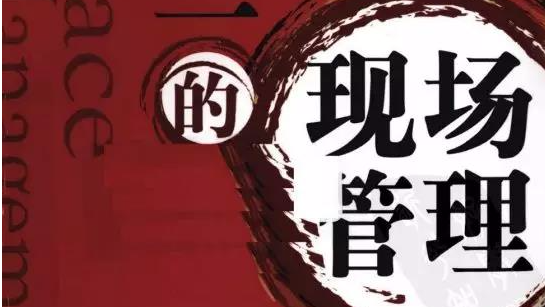
当前的金融危机和复杂的国际形势,以及互联网技术带来的社会生态和经营环境的巨变,使家具企业面临着前所未有的挑战。正如从其他领域跨界家具业的朋友所说:家具行业作业太传统了,这个行业所遇到的问题和二三十年前电子、汽车行业所遇到的问题,有着很多相似之处:
1.生产缺乏计划性,灵活性差;
2.设备故障率高,保养和维修工作欠佳;
3.生产线运行不均衡,产量波动大;
4.人员安排不合理,缺勤率高;
5.废品率或次品率高,返修工作量大;
6.换模时间长,生产批量难以下降;
7.运输距离长、运输方式不合理等。
······
家具企业现场的普遍现象
有这么多问题存在,并不意味着家居业存在全都是危机,相反蕴藏着涅槃重生的机会与可能。那么,如何实现自我救赎?
答案一定是通过科学先进的生产方式,消除一切无效劳动和浪费。通过把目标确定在尽善尽美上,不断地降低成本、提高质量、增强生产灵活性、实现无废品和零库存等手段,确保企业在市场竞争中的优势。一、改善应该先从“不花钱的改善”做起
企业在生产过程中常出现一种情况:当发现某工序是整条生产线的瓶颈时,我们最直接的实际想法/做法就是购买设备,而不是去检查有没有浪费的作业,想方设法消除浪费作业,更不是动脑筋朝低成本自动化的方向去改善(因为动脑是非常难受的一件事,需要我们跳出自己的舒适区),往往想通过购买全自动自动化设备,抹平瓶颈。
设备只能解决单点的问题,且生产流程都要围绕着这台先进的设备转,进一步带来了诸多垃圾流程,很可能因为我们的零部件质量一致性差、技术人员技能不足等诸多原因,导致设备使用艰难,需要很长的适应期或者设备根本无法适应。
因此,改善应该先从“不花钱的改善”做起。精益生产的奠基人大野耐一先生在《大野耐一的现场管理》一书中强调,在改善的过程中,首先考虑的不是购买设备,而是最佳的工作方法。就改善的顺序而言,应该首先进行作业改善然后根据作业改善的结果,再去考虑设备的改善,使之与作业更加配合;最后进行工序的调整改善,这才是打开改善思路之门的正确方式。通过学会怎么发现问题、分析问题、改善问题、保障问题不会发生才是真理。这种生产方式就是精益生产,这种管理就是精益管理。
大野耐一著作:《大野耐一的现场管理》
二、精益生产必将是企业实现自我救赎决胜措施
精益生产(LeanProduction,简称LP)是美国麻省理工学院数位国际汽车计划组织(IMVP)的专家对日本“丰田JIT(JustInTime)生产方式”的赞誉之称。精,即少而精,不投入多余的生产要素,只是在适当的时间生产必要数量的市场急需产品(或下道工序急需的产品);益,即所有经营活动都要有益有效,具有经济性。
精益生产被誉为是当前工业界最佳的一种生产组织体系和方式。因此,中国的家具企业,无论承认或不承认,认识还是没认识到,精益生产必将是企业实现自我救赎决胜措施。
在推行精益管理过程中,可以被使用的管理工具非常多,结合家具行业的特点可以将精益工具从以下使用场景进行分类:
发现问题工具-八大浪费
三、践行精益生产不能找理由
这些方法和工具看起来十分复杂和深奥,实际上在具体应用中并不困难,作用也十分明显。真正困难的在于企业实行实践上述工具的决心和毅力,困难与突破点在哪里?——践行精益生产不能给自己找理由。
精益生产被国内制造业引进大概在1980年前后,至今已有40个左右的年头,我们在推行精益的过程中遇到了各种各样的困难和障碍。很多时候,我们总喜欢把其归咎于文化、国情、行业特点等等外部因素,可是只有真正了解了TPS的发展历程才会发现,我们遇到的这些丰田都遇到过。甚至几十年前丰田面临的挑战比我们多的多。可是为什么他们会具有这种“朝着目标,坚持不懈,永不放弃”的坚定信念呢?
学习丰田的精益生产,不仅要学会他们的工具方法,还要深入地了解这些工具背后的原则,前后的因果逻辑关系,怎么样打破制约、创造条件,才能体会到“消除一切可能的浪费”的精益理念,进而渗透到企业日常工作的点点滴滴之中,这才能真正学到他们的思维方式。
在接下来的“精益生产”专栏中,我们将从不同层面展开,继续探讨家居企业实行精益生产的方法和步骤。
深圳市家具行业协会在企业开展精益生产活动
本网站仅为行业交流分享平台,转载请尊重原作者权益,如需转载请注明中华整木网(www.cnzhengmu.com)