内忧外患”的关键节点,精益生产是家居企业的竞争力第一课
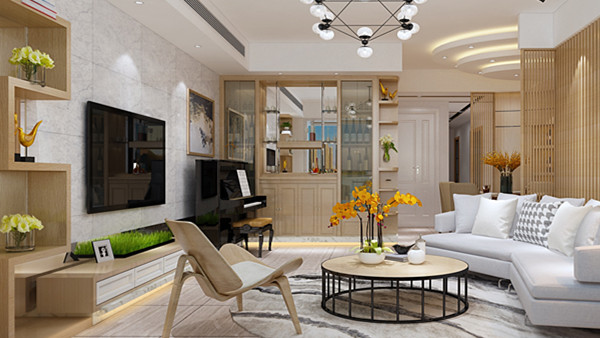
【中华整木网】工艺的改进、机器设备以及工业软件的提升等,是家居业转型升级不可缺少的条件。
然而仅有这些外力帮助还不够,企业内部的管理水平和生产效率往往决定了先进工具的最终效果。
实际上在家居业长期快速发展的过程中,许多问题被掩盖了。当大部分家居企业忙于渠道拓展、产品开发,内部的短板往往不太容易被注意到,尤其是生产过程中的浪费、低效甚至无效工作,无形当中让企业损失了许多利润和竞争力。
当前的家居业正处于“内忧外患”的关键节点,外有来自地产、家装等上游产业的抢食,内部则是行业集中、竞争加剧的淘汰赛。如何在这样的环境中求得生存和发展?
既然外部环境无法改变,或许内部可以成为突破的方向。“精益生产”正是被许多行业包括一些优秀家居企业所成功验证,帮助企业提升内部生产效率的绝佳方法。
也正因如此,本期《今日家具》将“精益生产”作为一个重要部分,希望能让行业再次重视这一理念,从粗放式发展逐渐转型为精细化运营,从内部开始提升效率和生产力。
它不一定“立竿见影”,但一旦得以贯彻实行,将为企业带来源源不断的“发展红利”。
精益生产将为企业带来哪些改变?
企业竞争中有两种方式可以获得领先优势。一种是通过产品或服务上的创新实现差异化,从而赚取超额利润,这方面的典型代表就是苹果手机;另一种方式,则是做到成本领先,不断降低产业链上各个环节的成本,从而获得竞争优势。
在家具业,绝大部分企业在成本降低上仍有着巨大空间,这将成为拉开企业之间差距的一道隐秘却坚固的墙。从许多方面来说,精益生产给企业带来的好处是显而易见的。
从提高生产周期的角度来看,假如某家具企业的年产值为1亿元,生产一套成品家具的周期需要30天,以每年300个工作日计算,则企业从生产资料到产成品每年仅有10次周转。
而通过实施精益生产,企业的生产周期缩减到了20天,在上述相同的情况下周转率达到了15次/年。
按企业的净利润率5%来计算,提高周转率后企业用同样的时间实现了1.5倍的产值,净利润也从原来的500万(1亿元×5%),达到了750万元(1.5亿元×5%),从而为企业直接创造了250万元的利润空间。(见表1)
再从产品合格率来看,在实施精益生产之前某沙发企业的产品合格率为85%,该企业每年需要生产2000套沙发。
假若每件次品所消耗的原材料和人工、水电以及返厂维修等综合成本为1200元,那么每年企业因为次品而损失的金额就高达36万。而通过实施精益生产将合格率提升到95%,则每年可直接节省的浪费金额就达24万。(见表2)
从以上简单对比中可以看出,在生产过程中的各个环节精益生产都有着很大的发挥空间。
尤其对于相对容易建立标准化作业的沙发、床垫企业来说,越早实施精益生产,带来的效果就越明显。
精益生产:多种工具的综合应用
精益生产最初源于早期的日本丰田生产方式(TPS,Toyota Production System),由美国麻省理工学院及其研究团队对全球丰田工厂进行研究总结后提出。
它以顾客需求为拉动,以消灭浪费和快速反应为核心,使企业以最少的投入获取最佳的运作效益,提高对市场的反应速度。
相对于标准化和工业化生产的汽车行业,精益生产在家具业的应用有着更高的难度,尤其实木家具生产中的应用相比板式定制难度更高。
而要实现精益生产,保持生产过程的“流动性”非常重要。
一般来说,将机械加工、喷漆涂漆、组装等环节进行分类组合是常用的方法。
例如,对家具或木料进行加工的封边、开槽、钻孔、雕刻等各个工序连续排列在一起,让某一套家具从投料到成品的搬运距离尽可能短,布局尽可能紧凑。而对于一些订单量大的产品如某种椅子,还可以采用专线生产的方式。
此外,在流水线划分的基础上,还可以让不同的生产工序尽量按照同一个“节奏”生产,保证上一个生产流程和下一个流程可以同步对接,也就可以减少半成品或成品的库存。
而通过对于库存和生产线的精益管理,还将进一步可以实现拉动生产,也就是下游生产环节(如喷漆)向上游生产环节(如机加工)提出需求,上游工序按需求生产,最终实现及时生产(JIT)。
实际上,精益生产需要配合多种工具的应用,如看板管理、拉动生产(PULL)、标准化作业(SOP)以及价值流分析、5S管理、全面生产维护(TPM)等等。
而精益生产的过程更是全员参与的过程。只有员工主动积极的参与其中,精益生产才有可能顺利的推行,这既是一大关键,也是一大难点。
精益生产,从消灭浪费开始
精益生产的另一大核心,就是“消灭浪费”。浪费就是从原材料开始到最终产品或服务为止,在每一个流程里不创造价值的活动,如等待、停滞、检查、做错、返工、修补、重做、滞销、退货、补件等,都是显而易见的浪费。
有些浪费是看不见的,如流程不良的问题,超过顾客需要的过度设计,工艺设计不合理的问题,物流方式低效的问题,员工消极怠工的问题等,这些隐性的浪费对企业的危害更大。
丰田汽车公司的生产主管,也是精益生产方式的主要创始人大野耐一认为,站在客户的立场上,只有五种增值的工作。它们是:
1、使物料改变:如裁皮,裁切板材,切削木材,钉架,注塑等。
2、组装:如沙发企业的钉架,封板,粘棉,扪工等。
3、改变性能:如家具生产的胶合,涂装和表面装饰等。
4、部分包装:主要是科学、合理、高效和安全的包装。过度、低效和错误的包装都是浪费。
5、部分服务:如送货上门,上楼,并且上门安装,阶段性的保养,收费或免费的更换部分构件或软件的升级等,都是客户需要的服务。不是客户需要的服务都是浪费和无效的。
对于家具企业来说,未来的竞争是基于全产业链的竞争,企业的每一分钱都要用在刀刃上。企业首先做的是要发现浪费,这需要一系列的工具和方法。
而更重要的在于如何通过制度和规范的作用,让企业员工和管理者能够主动发现浪费、解决浪费。
持续改善,让管理更加高效
“改善思想之父”今井正明认为,解决问题有两种方法。
第一种是创新,应用最新的高成本科技,第二种是运用常识性工具,如使用检查表等不需要花很多钱的工具,这个方法被称作做改善。而改善,则正是精益生产的核心思想。
企业在生产中如何找到需要改善的地方?如何将改善的成果持续?可以借助较为直观的工具——PDCA循环和SDCA循环,这两个循环也是改善过程的两个步骤。
PDCA循环又称“戴明环”,即计划(plan)、实施(do)、检查(check)、改善(Action),它从建立改进目标开始,经由执行、过程检查以及执行新的动作为一个循环,并反复进行。
而SDCA(建立标准standard、实施、评价和改善)则是将以上方法步骤进行固定、标准化,形成稳定的循环。可以说,前者的目标在于将现有流程进行改进,而SCDA则强调维护、保持。在改进、标准化、维持中,实现企业的螺旋式上升。
持续改善还包括其他策略工具,如ECRS分析原则、全面质量管理、全面生产维护、小组活动等。而改善的本质是通过培养员工成为问题解决者,而非单纯的任务执行者,来提升企业活力、赢得竞争的方法。因此,持续改善过程中员工的参与尤为重要。
此外,包括深圳家具开发研究院DEDE在内的专业机构,也在持续为行业普及精益生产的理念和实践,推动行业进步。
精益生产难以推行,是何原因?
对于精益生产大部分家居从业者可能不算陌生。但真正能够在企业推行并取得良好效果的却非常少。在向许多行业朋友询问为何推行困难时,我们收到了许多不同的答案,如:
有的人认为精益生产对于企业员工的要求太高,很难做到让每个人都有这么高的自觉性;
有的人认为是文化差异,源自日本的精益生产理念很难在中国社会扎根;
还有的人认为效果难以持久,往往在有外部力量协助时有效果,一段时间后又回归原来水平。
实际上,精益生产难以推行最根本的原因还在于企业管理者的认识不足,以及投入不够。在于大部分家居企业已经习惯于过去“赚快钱”的方式,而对于需要下很大力气、需要一定时间反复尝试的事情,一时很难接受。
正如顺德职业技术学院刘晓红教授所说,“纵观家具行业,最缺的不是设计,也不是市场,而是脚踏实地地抓管理、建标准、抓质量、降成本、增利润的工匠精神和做事态度,企业总是‘因善小而不为’”。
只有企业高层真正意识到粗放发展的时代一去不复返,未来是属于精益生产、精细化运营的企业,才有可能从战略的高度将精益植入到企业当中。
在这个过程中,通过动员全体员工、建立相应的制度规章,实行培训、阶段反馈总结,不断建立和提高标准,企业才算真正的将精益生产落到了实处,也才算真正走向成熟,迎接未来的工业4.0或智能制造时代。
来源:美国今日家具
本网站仅为行业交流分享平台,转载请尊重原作者权益,如需转载请注明中华整木网(www.cnzhengmu.com)