建材陶瓷“无人工厂”要来了!2025年全行业将再减员五成
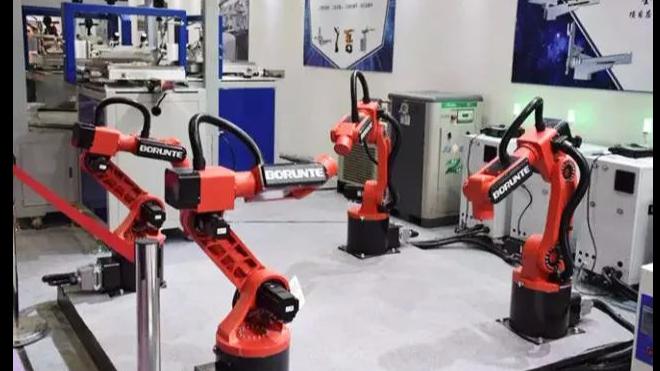
【中华整木网】中国陶瓷工业正阔步迈向“智造时代”。
近几年,身处转型风口的中国制造业面临的人口红利消失、生产成本攀升、产业亟待升级等压力日益紧迫,倒逼“智能智造”成为制造业的潮流代名词,在时代的裹挟下,我国陶机装备智能化亦迎来翻天覆地的革新与升级。
过去,由于生产的自动化程度较低,陶瓷一直被冠以“劳动密集型产业”,粗放的发展模式饱遭诟病。
进入“十三五”以后,我国陶瓷生产的自动化、智能化水平突飞猛进,人均产值显著提升,大量的生产环节实现高度自动化,并逐步向智能化、信息化迈出一大步。
据业内人士介绍,当前我国建筑陶瓷已经基本实现整线自动化,并搭建起智能化、信息化雏形,而卫生洁具虽然正处于自动化的快速推广与应用阶段,但未来几年的智能化发展亦十分可期。
不仅如此,在国家政策、产业背景、市场前景等一系列利好消息的助推下,我国陶机装备智能化、信息化技术与日俱进。兰科智能、多麦机械、贺祥机电、金马领科、新鹏机器人、光华智能等装备企业均表示,在今年6月18日举办的第33届广州陶瓷工业展上,将携带最新的“革命性产品及技术”璀璨亮相。
这让今年的广州陶瓷工业展亮点迭出,备受各方期待。
智能化生产初现雏形
工作人员按下操作开关,AGV堆垛机器人开始自动运行:叉起1立方米大小的木制托盘,倒车、转弯、前行,准确无误地将托盘运送到指定货位堆放,再原路返回到起点……重复循环,整个过程一气呵成,完全的无人化。这是近日佛山市光华智能设备有限公司成品车间出现的一幕。
“我们自主研发的AGV堆垛机器人,实现了盲导转向、裸码货物功能,有效解决了瓷砖打包入库最后100米的智能化,目前已经在大型陶瓷厂得到应用,缓解了企业的用工压力与成本压力。” 光华智能总经理霍丰源自豪地介绍。
相比传统的人工叉车,AGV堆垛机器人使用电能,无噪声、无污染,有助于实现洁静工厂和提高企业形象,同时通过“机器人替代人工”,可与企业管理系统连接,有助于企业实现精准入库、发货和数据分析,提高企业的数字化管理能力。
霍丰源说,发达国家陶瓷厂20年以前就已经普遍使用AGV,而我国才刚刚开始起步。目前,AGV在国内大型陶企的使用方兴未艾,根据陶企提供的研究课题和生产需求,光华智能正在着手研发搬运式AGV,以及进一步提升机器人的灵活性、工作效率和使用功能,协助陶企抢占智能制造先机。
光华智能的创新发展,仅仅只是当前我国陶机装备智能化如火如荼的一个缩影。放眼整线生产,近几年我国陶瓷“智造”取得的发展成绩更加炫目。
以工序最繁杂、劳动力最密集的窑后为例,磨边、质检、包装、码垛、仓储等环节近几年正快速实现智能化。譬如包装环节,在陶企降成本、减人工、柔性化生产的现实要求下,发展速度一日千里。过去一条生产线的包装环节往往需要十几名工人,而现在仅需两三名工人就能够轻松完成,未来几年大有可能实现一个工人看管多条线。
与此同时,在包装过程中,采用更先进的包角方式,不再需要泡沫,进一步降低了成本和变得更环保。此外,早期的打包机不能转换规格,现在一台打包机能够转换近10种规格,设备越来越灵活。
检测环节的智能化亦快速推进——激光检测机正逐步由实验室走向陶企生产车间。在瓷砖大产能生产线“大干快上”的背景下,产品生产的速度加快,靠人工检测和传统检测机容易遗漏很多品质问题,而激光检测机能够对瓷砖表面的裂痕、斑点、凹凸、缺陷、色差等进行快速系统化检测,在实现减员和提高工作效率的同时,大大降低检测的误差率。
众多行业人士表示,瓷砖生产的智能化、信息化已经初步成型,并在一定程度上实现了“小批量、多订单”的柔性化生产。未来的方向是在现有基础上持续创新,不断的完善与升级。
对比瓷砖行业取得的辉煌成绩,卫生洁具的自动化、智能化发展略显落后,行业整体正处于大刀阔斧的自动化改造阶段。不过,据多家上游装备企业介绍,以目前国内的技术储备,洁具生产60%~70%的环节都能够实现智能化,包括施釉、修坯、AGV等。
唐山贺祥机电股份有限公司总经理赵祥来介绍,以贺祥目前的技术实力,在卫生洁具生产的高压成型、机器人涂胶、搬运、干燥、喷釉、烧成、包检等环节都能够实现智能化。如高压成型机设备,已经具备保养提醒、故障自诊、产品是否达标等提示功能。
但即使如此,卫生洁具行业还远无法实现整厂的物联。究其原因,卫浴行业产业基础相对薄弱、标准化程度低,智能化发展的难度更大。由于缺乏标准化生产,时常出现“同一批原料,不同季节、天气,成品合格率不一样”的问题,这给机器人的使用带来巨大挑战。
在佛山市新鹏机器人技术有限公司总经理秦磊看来,陶瓷行业的智能化发展已经取得了一定成就,当下及未来最紧迫的是实现整厂的信息化,例如设备的耗电量高低、工人操作是否合理、保养情况如何等,都需要经过信息化的手段进行数据采集和分析,最终实现节省成本、延长设备使用寿命的目标。
当前,信息化的现状是,企业能够采集一部分数据,但无法对数据进行快速、准确的自动化分析,以及对企业的生产安排提供参考建议——这显然难以满足陶企的发展需求。据预测,陶瓷行业要实现真正的信息化,至少还需要5~8年时间的沉淀。
蒙娜丽莎陶瓷自动化打包线
“无人工厂”逐步由设想变为现实
最近两年,伴随着陶瓷行业结构调整的深入、智能化设备及技术的逐步完善与成熟,以及产业变革与升级的迫切需要,无人工厂、智能仓储等正在由设想转变为现实。
2017年3月21日,重庆唯美陶瓷有限公司正式投产。据悉,投产的重庆唯美一期一号主车间第一条生产线,长度为1500多米,只有50名工人,线上的所有作业环节均实现了“机器代人”,工人只是负责操作机器。
2017年12月6日,新明珠陶瓷集团绿色智能制造示范工厂在肇庆高要禄步工业园落成。从配料到自动打包入库,其中的12个步骤,工人只需在控制室里轻按按钮,就可以完成整个生产过程的控制;控制室外面,整个车间噪音小、宽敞明亮、通风透气、无尘,只有两三名工人在巡视设备;通过激光打码方式,每一片砖都可实现从原料到生产工艺的流程追溯。
新明珠陶瓷集团绿色智能制造示范工厂,员工在操控平台上作业
2018年12月23日,冠星陶瓷企业清远生产基地立体式智能化仓储中心建成投入使用。该仓储中心进出仓作业全程由智联云系统智能控制,自动打包、智能输送入仓,再到出仓装成,全程仅耗时10分钟。相比人工成本高、占地面积大、搬运困难复杂的传统平板仓,有效提高了产品进出仓效率,降低了产品破损及人工成本。
上述案例只是“冰山一角”。在智能化、自动化设备的应用上,如今更多的陶企开始积极引进。
广东金马领科智能科技有限公司销售总监许文杰回忆,2013年的时候,绝大部分卫生洁具工厂连自动化设备都没有,更甭提智能化。“当时的洁具厂生产,基本靠人力,厂房内粉尘飞扬,闷热潮湿,作业环境极其恶劣。”
但随后几年,在各方经营压力倒逼下,卫生洁具行业的自动化、智能化迅速铺开,不少卫浴企业主动联系设备供应商,对工厂进行自动化、智能化改造升级。如今,部分大型卫浴企业已经实现了二维码流程追踪,以及仓储的智能化、信息化管理等。
其中,施釉机器人的发展较为亮眼,短短几年时间,就在国内得到快速的普及应用。据不完全统计,2015年卫生洁具行业几乎没有企业使用施釉机器人,但现在在线使用的施釉机器人已经达到700~1000台。
佛山多麦机械设备有限公司设计顾问邓焕常亦表示,当前越来越多的陶瓷厂开始清晰地认识到,自动化、智能化发展是大势所趋。为了更好地吸引高质量人才,优化工人的年龄结构;更好地运用大数据管理,紧密契合未来新时代消费者的需求,越来越多的企业不惜投入重金,全力实现智能化生产、信息化管理。
一个可供佐证的变化是,过去瓷砖厂的打包环节基本以人工为主,而现在智能打包机在全国各大产区得到了广泛应用,不少小厂也积极引进相关设备。同时,数据采集分析、“一砖一码”等技术愈加成熟和加快普及,很多陶瓷工厂即便没有使用智能仓储,亦能够在一定程度上实现数据分析。
对于智能化发展推波助澜的利好消息是,国家政策给予机器人制造等智能产业的扶持力度更大、融资环境更好,税收更优惠。并且,各地方政府亦大力鼓励陶企对工厂进行智能化升级与改造。
中国建筑卫生陶瓷协会常务副会长缪斌坦言,按照当前的发展速度,预计未来3~5年内,更多类似于新明珠和唯美的智能化生产线将在全国各大产区或主要企业投产。这些新生产线普遍只需要配置五六十名工人,更先进的甚至只需二三十人。
智能化加剧陶业“马太效应”
智能化、信息化高速发展的背后,是陶企对生产成本极致管控的经营需求。
在过去粗放发展和供需平衡的年代,陶企之间的竞争,更多是比拼品牌和产品,而当前各项生产成本急剧攀升,供需关系严重失衡,成本控制成为缔造陶企核心竞争力的重要方向。
据陶机装备行业人士分析,智能化、信息化是陶瓷产业发展到当前阶段的必然。过去几年瓷砖行业已经实现高度自动化,奠定了实现智能化、信息化的扎实基础,同时在成本管控方面,瓷砖企业最大的成本实际上是管理成本,包括效率问题和浪费问题等,而这些必须通过大数据分析、工业互联网等技术才能得到有效解决。
围绕这一方向,装备企业开启新一轮创新竞赛,不断提高设备的工作效率、智能程度,以及数据分析等能力。
佛山市兰科智能工程有限公司总经理李学峰介绍,兰科正在和大型机构、研究院展开深度合作,共同研发更智能的窑后设备。譬如,当前纸箱价格持续上涨,已经让很多企业不堪重负,下一步兰科计划推出更智能的打包机及辅助设备——陶瓷厂直接采购原纸纸皮,在打包环节实现所需纸箱的切割、印刷及包装,相当于省去了纸箱厂的中间环节,可大大降低纸箱使用成本。
兰科智能研发的自动缠膜设备
事实上,最近几年我国陶机装备智能化发展速度有目共睹,设备智能化程度每年都会在原有基础上迭代升级,呈现效率更快、质量更好、功能更全、精度更高等特征。
金马领科销售总监许文杰说,以金马领科的拳头产品“施釉机器人”为例,初期的目标是通过机器人将釉施到马桶上,第二阶段考虑的是怎么提高施釉效率,第三阶段则是将客户的需求满足到极致,做到更省人工、更高效率、更省釉料。从第一阶段到第三阶段,仅用了短短几年时间,下一阶段的方向是,提供标准化产品,结合企业的实际生产情况,让施釉机器人能够适应每一家工厂的生产环境。
在智能化迅猛发展的大幕下,中国陶瓷行业新一轮大洗牌暗潮涌动,行业分工与市场格局将全方位重塑,“强者愈强,弱者淘汰”的马太效应愈加凸显。
综合实力较强的品牌型企业,依托强劲的资本力量,大规模地引进智能化设备及技术,用以缩减成本、提高生产效率,实现真正的信息化管理。借助精准、详细、便捷的大数据分析,能够准确地把握消费需求,实时了解产品库存量、销售量,同时在精细化的管理及智能化设备的监测下,产品品质更加卓越与标准化,市场竞争力进一步增强。
而实力较弱的小型陶企,在生产由“传统工厂”向“智能工厂”升级过程中,囿于资金实力与发展远见,难以大面积运用智能化设备,导致生产成本居高不下,产品品质难以提升,品牌形象裹足不前,并且在掌握消费需求、内部管理、库存分析等方面始终处于粗放、低效率状态,发展空间捉襟见肘。
可以预见,在未来一段时间里,智能化水平将成为衡量陶企综合实力与竞争力的重要参照,行业准入门槛与集中度将进一步提升。
“中国制造2025”:再减员五成左右
“中国制造2025”是中国政府大力实施的制造强国战略,其中将智能制造作为主攻方向。由于近几年,在多方利好的助力下,我国工业机器人产业蓬勃发展,陶机装备智能化水平显著提升,这激起行业人士对“中国制造2025”的美好畅想。
虽然从当前的现状来看,我国陶机装备智能化才刚刚起步,关键零部件普遍依赖进口,技术储备低,应用规模小,生产的设备在精度、可靠性等指标上普遍低于国际顶级水平,距离真正的“无人工厂”任重道远。但也正因如此,我国智能化陶机装备产业潜力无限,前景广阔。
兰科智能总经理李学峰介绍,近两年我国工业机器人产业如火如荼,企业竞相扩产、资本持续注入,行业政策逐步完善,整体呈现健康发展态势,与国外的差距正在逐步缩小,甚至在部分细分领域已经超过国外,达到世界一流水平。
多位陶机装备行业人士对“2025中国陶瓷工业的智能化水平”表示出极为乐观的态度。均认为“到2025年,我国陶瓷生产整体素质将大幅提升,创新能力显著增强,全员劳动生产率明显提高,工业化和信息化融合再上新台阶”。
李学峰说,距离2025还有六年,六年时间内随着陶机装备智能化技术的突飞猛进,完全能够实现“一条生产线在现有基础上再减员60%”,整个工厂的信息化将全部统一,企业老板、生产厂长只需要拿着手机、点开APP,就能够知道精确的库存量、发货量,以及设备的使用状况、保养时间等数据。
多麦机械设计顾问邓焕常表示,到2025年我国陶瓷生产环境、面貌一定会发生翻天覆地的变化,陶瓷砖工厂在现有基础上能够减员5成左右,人力成本大幅度降低,智能化设备的功能、效率、外观、精密度等都将大幅度升级,生产工人真正实现由“传统普工”向“技术蓝领”的转变过渡,车间生产环境、厂容厂貌都将得到“质”的改变。
新鹏机器人总经理秦磊预测,2025年大型陶瓷砖工厂能够完全实现靠数据来管理工厂,而卫生洁具工厂的自动化亦显著提升,减员效果显而易见,以年产100万件洁具的工厂为例,当前普遍需要900~1000名工人,而到2025年可能只需要300~400人。
贺祥机电总经理赵祥来介绍,唐山卫生陶瓷工业自1914年诞生以来,距今已有105年历史,但一直采用传统生产模式和技术,直到最近三五年才真正发生革命性改变,未来三五年,在用工压力的倒逼下,变革速度还将进一步加快。“预计到2025年,国内一线卫浴品牌的智能化设备使用率将达到70%左右,远高于当前15%的普及水平。”
行业人士一致认为,2025年瓷砖生产的很多环节都将实现高度智能化,智能设备的大面积使用逐步由龙头企业扩散至中型规模企业。与此同时,随着信息化与数据分析能力的提升,未来原料、烧成、包装、码垛、仓储等环节将紧密串联,并能够归属到统一的控制室,进行集中监控、处理,真正开启数字化、少人化智造模式,真正摘除“劳动密集型产业”负面标签。
从发展前景来看,欧美、日本等发达国家建筑陶瓷、卫生洁具生产均已实现极高的智能化,国内汽车、家电、烟草等行业亦基本实现无人化。对比之下,我国陶瓷生产的智能化、无人化已经远远落后,亟需快速提升。
事实上,在顶层设计、国际竞争、人口结构、成本高企等各方面助力与压力下,最近几年我国工业智能化装备产业极速提升,并给予下游实体制造企业极大的自信与无限的升级空间。
或许到2025年,我国陶机装备智能化发展速度比预期更快;亦或许在不久的将来,陶瓷工厂管理者只需要坐在办公室、喝着茶,就能够轻松管控一家大型工厂。
本网站仅为行业交流分享平台,转载请尊重原作者权益,如需转载请注明中华整木网(www.cnzhengmu.com)