实木定制设计与生产的瓶颈如何突破?听2021实木智造大会名家论道!
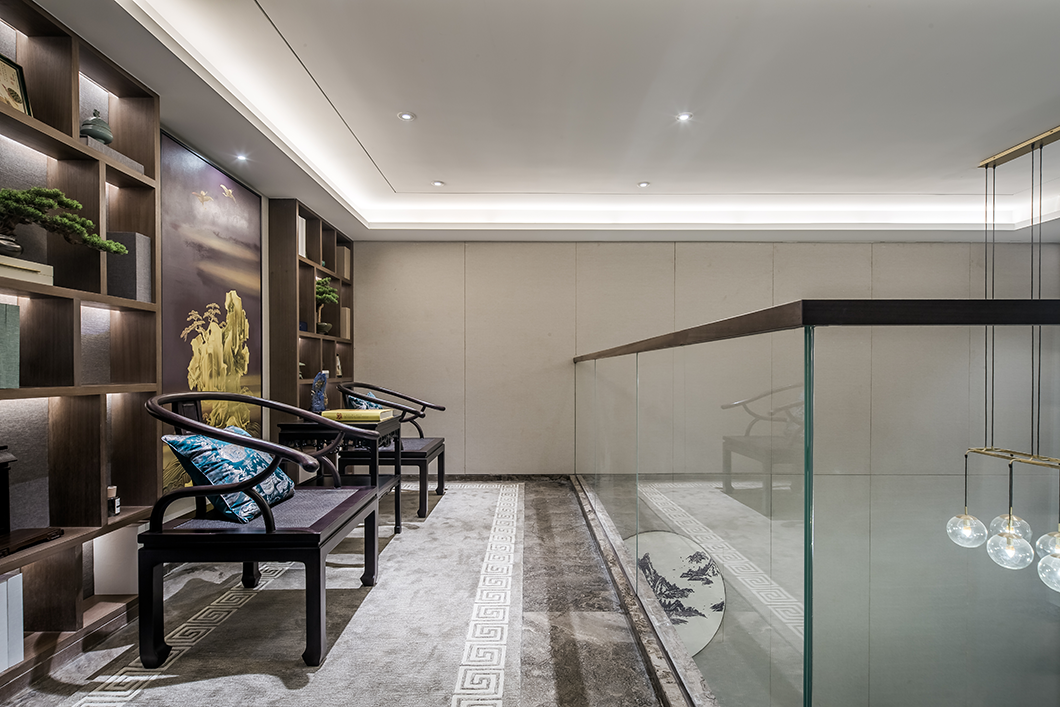
作为占有细分市场的实木家具,面对有较成熟的模块化、标准化系统支持的板式定制家具,也在同步进行产业升级。在实木家具走向定制时代的过程中,实木设计与生产都面临多方难题亟待解决。
01 实木定制家具企业目前存在的问题
实木定制是一个系统工程,任何环节都非常重要,尤其在设计和生产两个环节,实木定制企业普遍遇到以下问题:
01-1 设计阶段存在的问题
①已有产品没有完善的结构图纸,已有产品数据库搭建不完善
该情况导致客户下单后,尺寸细节修改的环节过于复杂,人工绘制图纸的时间长,客户等待修改的时间也长。
②已有产品缺失标准化的结构、部件或尺寸模数,系列衍生困难
作为定制家具产品,更加注重客户的个性化需求,按需修改尺寸成为很多已有产品的必经之路,但由于现在产品的分类,编码都未制定标准, 尺寸变化的规范也未完善,导致客户定制的产品无法融入标准生产线,对后续生产过程造成了影响。
③拆单环节普遍人工操作,自动化程度较低
由于本身产品的定制属性和非标准,设计制图人员只能人工进行拆单并绘制各个零部件,该环节不仅考验设计师的结构设计能力,也需要长久的经验。拆单出错率和设计阶段的耗时难以降低。
01-2 生产阶段存在的问题
①受木材特性限制,备料环节复杂
实木作为一种天然材料,具有各向异性、干缩湿胀的特点,实木的性质导致定制家具造型有局限性,多数定制集中于异形件造型本身,或柜类家具的功能划分上。此外,在人工选料过程中实木缺陷标记易错率较高,返工率较高。
②信息化落后,产品链联接不紧密
目前企业生产单项技术信息化虽已实现,但从图纸到各加工设备之间的传输多为人工处理,修改细节尺寸也直接由技术人员在图纸上手绘修改,设计部门和生产部门的图纸对接不及时,生产管理与监控也无法快速实现。
③实木部件品种繁多,结构部位差异性大
在同系列产品中部件造型需要有呼应关系,而实木家具零部件的互换性较弱,并且同造型不同材质的生产,导致结合方式发生变化,从而生产线变得更为复杂。
02 实木定制突破瓶颈的思路借鉴
针对上述提出的实木定制家具企业现存的一些问 题,主要可以通过以下几个途径进行解决:
①引进成组技术,对实木零部件进行标准化、系列化的设计。
标准化设计是指在产品设计开发阶段制定相关的 标准,统一要素,面向产品的通用性,采用共性条件,开展的适用范围比较广泛的设计,加速产品设计开发的速度。
通过产品的标准化组合,提高产品零部件通用性、标准化的程度,使产品的设计开发获得较好的经济效益。而产品系列化是标准化走向成熟的标志;系列化是使某一类产品系统的结构优化、功能最佳的标准化形式。
②引进智能生产系统,提高信息化、智能化水平。
实木定制家具从原料端开始搭建网络系统,并搭配使用相应的可识别信息的工艺设备,已有企业针对实木定制家具设计端、生产端、安装端进行了信息化搭建的研究,同时通过智能生产技术的引进,如智能优选锯切、无人化缺陷扫描、智能指接技术、高频拼板技术等,使实木定制生产高效化、规模化。
③实木家具分阶段引入编码技术,逐步实现智能制造。
从备料到机加工到包装运输,在成组技术引入的基础上,对已标准化的实木产品零件进行编码,生产线各工段、各加工机械扫码执行加工工艺。如根据 产品零件规格指导拼板、选料,按成组零件进入加工周转箱,周转箱携带编码,加工机械和生产线各节点扫码 执行操作等。
④提高企业员工的信息化素养,重视研发与生产等部 门之间的信息交流。
全体员工需要进行相应的培训,熟知企业标准化信息,对企业生产链有深入的了解。搭建各部门快速交流的平台,必需人工录入的流程也能及时反馈给相应部门,保证各环节信息的良好对接。
随着实木家具走向智能制造阶段,实木家具客户群的个性化需求也将逐渐通过标准化、信息化得以实现,实木家具企业也将面临更加多变的客户需求。零部件标准化是解决实木定制设计生产的关键条件,在设计、生产、物流等方面将会发挥积极作用。
9月15日,围绕「成品家具转型定制」过程中面临的种种问题,2021国际名家具机械材料展,将在东莞厚街·广东现代国际展览中心,举办以「拥抱趋势 木遇新生」为主题的中国实木智造技术创新大会。
届时,南京林业大学、中国林业科学研究院、鲁班园等机构及国内实木企业将齐聚东莞,为行业解惑答疑、献计献策,还有知名学者、工程师、生产专家分享最新的生产研究,论道实木转型之路,助力企业打破瓶颈、对话2021!
本网站仅为行业交流分享平台,转载请尊重原作者权益,如需转载请注明中华整木网(www.cnzhengmu.com)